More about LeSS manager
It is an oversimplification to understand that LeSS managers mean less (fewer) managers. The more common change in my experience of LeSS adoption is to transform the manager role. Therefore, let's talk more about this "new" role.
Managers improve organizational capability
In the LeSS guide "the LeSS organization", there is the below picture that maps the roles and responsibilities to the focus areas. Managers focus on organizational capability improvement.
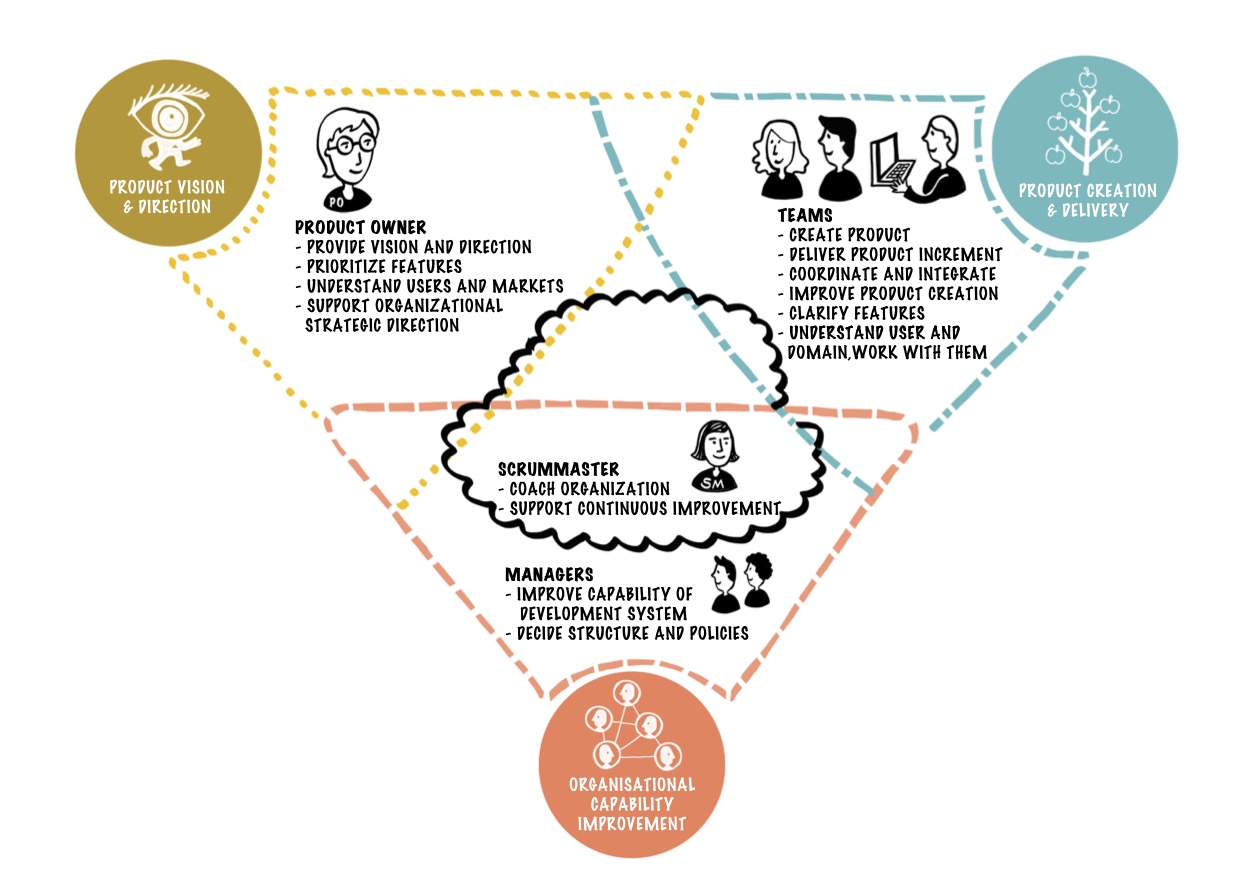
One of the clients I worked with actually calls their managers as capability manager, which reflects well their focus area. On the other hand, traditional functional managers may also focus on competence and capability. For example, they may coach and teach the teams in improving their development capability. This is great, however, the organizational capability is more than that. As defined in LeSS rule, "managers' role is to improve the product development system by practicing Go See, encouraging Stop & Fix, and 'experiments over conformance'." Product development system integrate people, process, technology, and more.
Let's elaborate a bit on these means to improve the product development system.
- practicing Go See. "Go see for yourself at the gemba (real place of work) to thoroughly understand the situation" is the 12th principle in the Toyota Way - 14 principles. It is the foundation for effective continuous improvement. There are two kinds of gembas: 1) the gemba of value consumption, where the product is used; and 2) the gemba of value creation, where the product is created. Unfortunately, many managers, especially middle managers, stay away from both gembas. Instead, they live in the powerpoint world with an illusion of reality.
- encouraging Stop & Fix. "Build a culture of stopping and fixing problems to ultimately build quality in" is the 5th principle in the Toyota Way - 14 principles. Quick fix is a norm for many organizations. Without deep analysis, we act based on the symptoms, thus recurring problems. Managers need to be the role model for stopping and fixing, and coach others to do so.
- "experiment over conformance". This is from lean thinking as well. Rather than forcing conformance to central processes, and to bad or outdated product and technology decisions, managers challenge the status quo, and experiment in various areas of product development system to learn and improve.
Should managers improve organizational capability on their own? If managers do all the improvements while others follow, this conflicts with self-managing teams and the desire to unleash the potential of everybody in the organization. Therefore, managers should enable improvements by coaching teams and growing people. On the other hand, how can managers coach teams without themselves deeply doing improvements? Therefore, managers should do the improvements themselves too, preferably in the area of organizational structure, decision and policies.
Managers teach thinking skills
In the LeSS guide "managers as teachers and learners", it is expected that LeSS manages learn to have a good understanding of both the domain and current technical skills, then use that to coach and teach the team. There is another LeSS guide "both domain and technical capability", emphasizing that the right balance between technical skill and domain understanding is needed.
These guides are consistent with what is expected of lean managers - to be hands-on masters of their domain of work. However, lean managers are further expected to understand lean thinking, and to spend time teaching and coaching others. Its focus on thinking skills is evident in Toyota's internal motto "good thinking, good products".
The thinking is embedded in the continuous improvement, and the coaching for better thinking must happen in the real improvement too. Learners learn about the thinking through practicing improvement kata based on PDCA; while coaches coach about the thinking through practicing coaching kata. These two katas go hand in hand, as shown in the below picture from Mike Rother's toyota kata website.
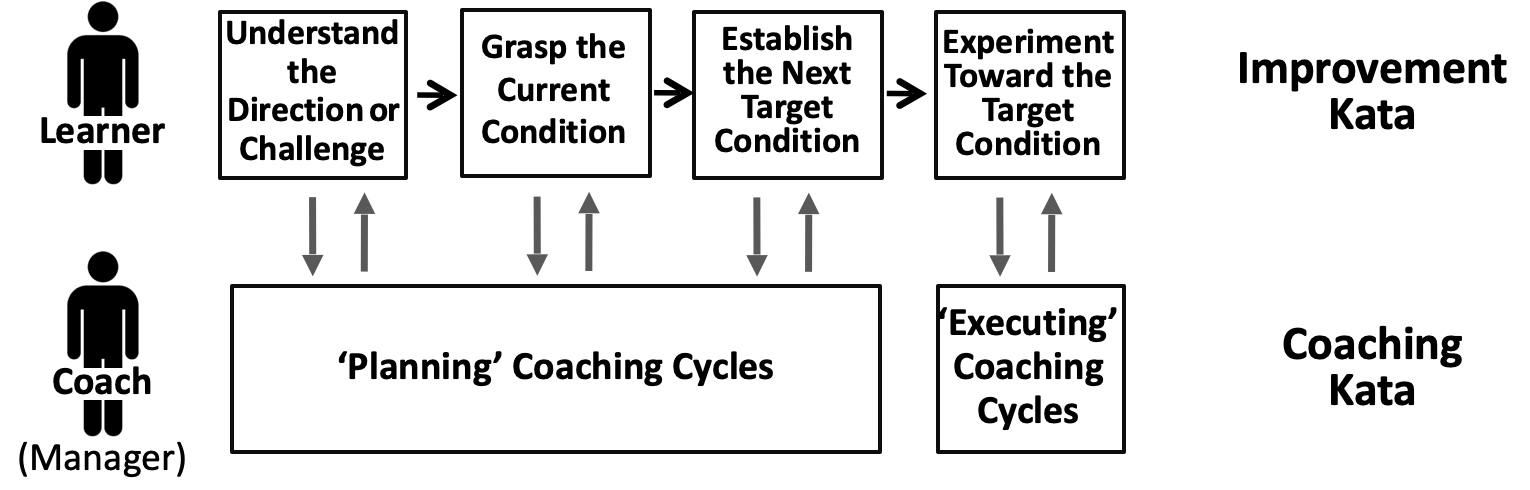
It looks as if managers mainly coach, thus only need to practice coaching kata. This is not true in many organizations, as managers first need to internalize the lean thinking, such as go see and stop & fix, via practicing improvement kata themselves, until they can shift the focus from doing to coaching.
This aspect of manager as teacher may present a great challenge for the transformation of the manager role, as many managers want to be managers, not teachers.
Managers build learning organization
Systems thinking is one of the LeSS principles, and we say that LeSS managers need to be systems thinkers. In my view of "from LeSS to learning organization", LeSS managers go beyond systems thinkers, as systems thinking is the fifth discipline, and there are other four disciplines. LeSS managers are the builders of learning organization, via practicing all five disciplines and coaching other to practice.
The below picture shows the three aspects in learning organization, supported by five disciplines.
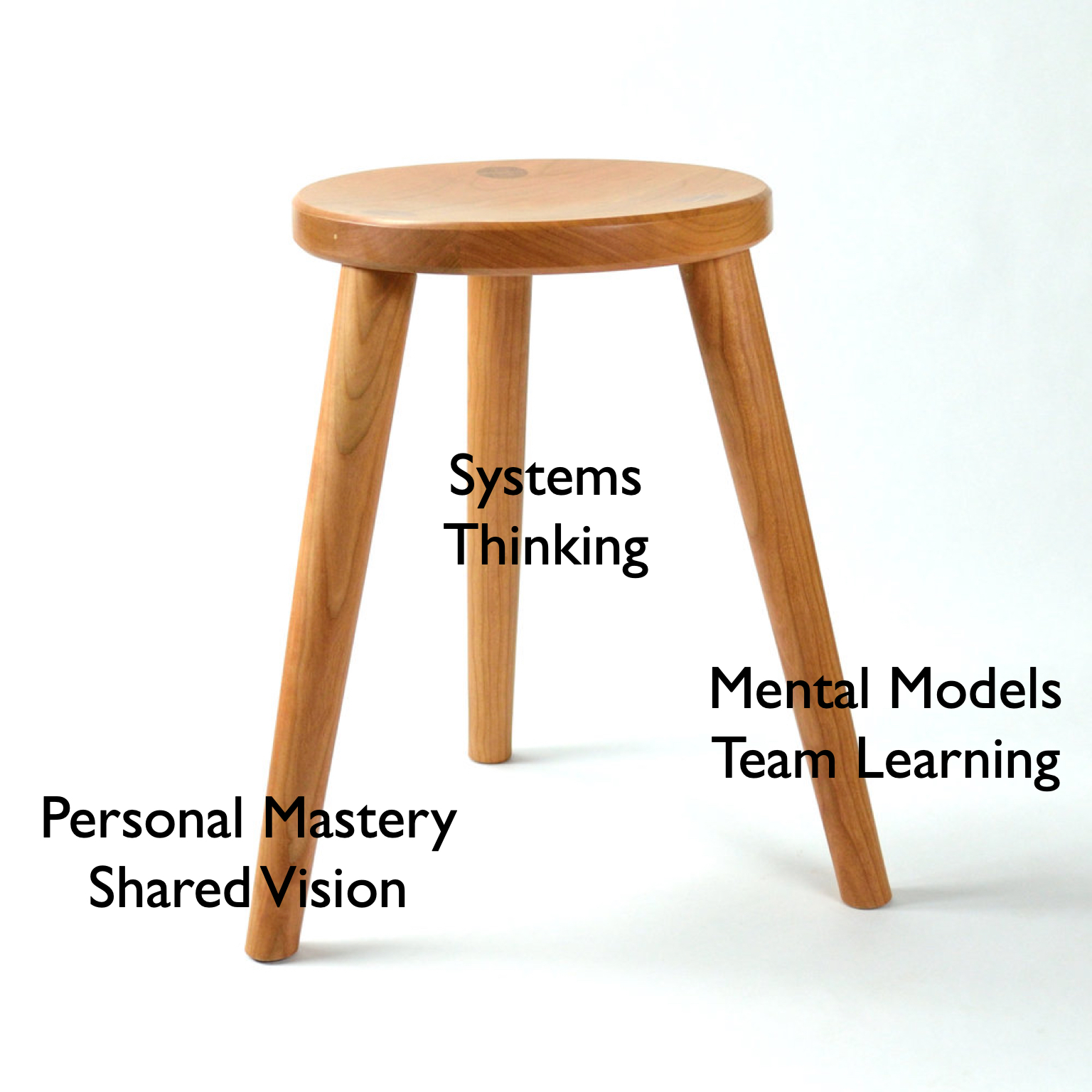
- Visioning, via personal mastery and shared vision
- Learning, via mental models and team learning
- Thinking, via systems thinking
Applying these into product development organization, I made a distinction between product learning and process (including team and organization) learning in the "How does LeSS optimize organizational ability to learn?" article. In a LeSS organization, PO and teams focus more on product, while SMs and managers focus more on organization. Therefore, LeSS managers focus on organizational vision and improvement.
- They personally envision the future state of organization and facilitate the emergence of shared organizational vision. See more in the "Shared vision on organization" article.
- They participate in overall retrospectives for organizational learning and improvement, and challenge the existing assumptions and beliefs so as to improve mental models for both own and others.
- They practice systems thinking and coach others to practice. They may start from deepening the analysis in PDCA, then expand it to systems modeling, as introduced in the "Practice Systems Thinking: 2) from Fishbone Diagram to Causal-Loop Diagram" article.
Conclusion
What is the theme for LeSS managers? They improve and coach others to improve; they learn and coach others to learn; they experiment and coach others to experiment. In fact, improving, learning, and experimenting are the same thing. In a nutshell, LeSS managers constantly develop themselves and develop others.